Solutions for the industry
INDUTRAX in production
The use of our software in production
Reduce buffer stocks, eliminate unnecessary routes and search times, avoid errors right from the start: Our software provides you with more efficient throughput and smooth production processes. Make well-founded, data-based decisions and continuously improve your processes - with user-friendly interfaces and mobile apps.
Directly on the order: dynamic, paperless order information
Information on a production order changes over the course of the product creation process. With e-labels, this information is adapted to the situation, at the touch of a button or by rule, and digitally available directly on the order on the store floor. Notes on processing or clarification requirements are displayed immediately. This drastically reduces errors during production and eliminates all paper and printing costs. This is how you avoid errors.
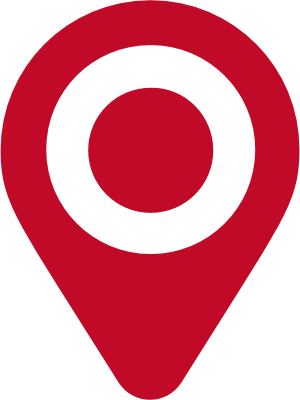
- Real-time visualization of object information on e-labels for transparency about production statuses
- Customised designs and data content
- Process-based updating of the E-Ink displays
- Integration of Pick-To-Light to indicate the need for action
- >Feedback and confirmation of instructions at the touch of a button to indicate the need for action
Read our 1 × 1 of time saving in logistics!
Automatic recording of work in progress: tracking work in progress
The more transparent the entire production process is, the fewer buffers and safety stocks are required - and therefore the lower the total circulating stocks.
This means that less space is required for temporary storage, unnecessary transportation and searching is avoided, thus saving tied-up capital and increasing liquidity. This simply saves money.
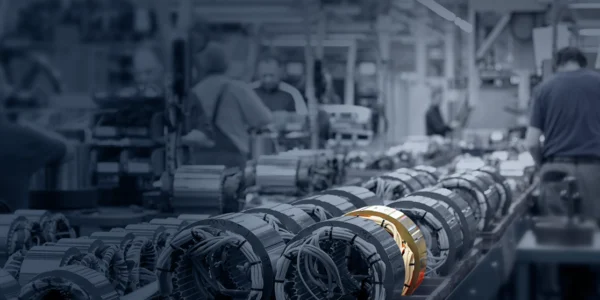
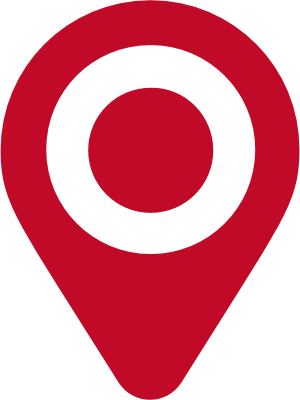
- Dynamic determination of the status of the value stream
- Real-time display of the location of materials, components, assemblies, semi-finished and finished products
- Automatic mapping of locations to value-adding and non-value-adding process steps verifiable value stream analysis
- Rules for automatically booking the start and end of a process step in the production control system
Process monitoring and process control: detect errors in real time, automate bookings
Detect irregularities in the production process at an early stage and prevent process interruptions. Errors are also visible in real time - you can initiate countermeasures immediately.
Automate manual documentation and minimize non-value-adding activities. This increases your throughput. This is how sustainable optimization works.
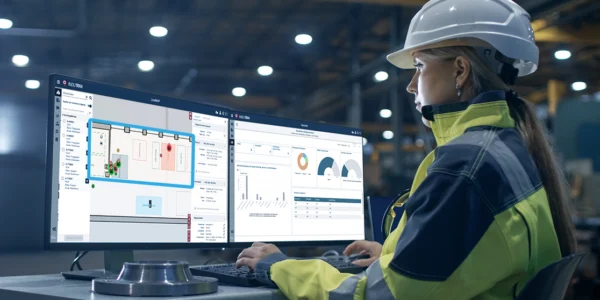
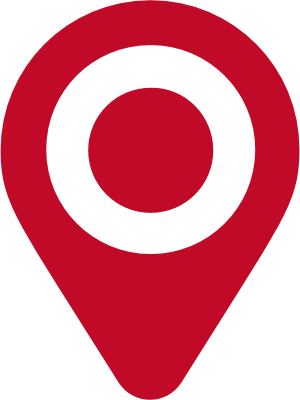
- Automatically synchronize orders from Manufacturing Execution System (MES) and Enterprise Resource Planning (ERP)
- Manage individual orders or order lots in an order hierarchy
- Automatic booking, e.g. when placing an order with a quality problem or when transporting an order to the dispatch area
- Automatic tracking of dwell times in buffer areas and in process steps
- Comparison of process plan and process flow
- Rules for automatic notification in the event of delays
- Better estimate the effects of rescheduling on the entire production process
Is there already a use case for you here?
Continuous improvement process
By recording the history of material flows, our software identifies any potential for improvement.
This allows you to address bottlenecks (error-prone process steps), optimize process planning and increase efficiency and throughput. And that continuously for ever more improvements.
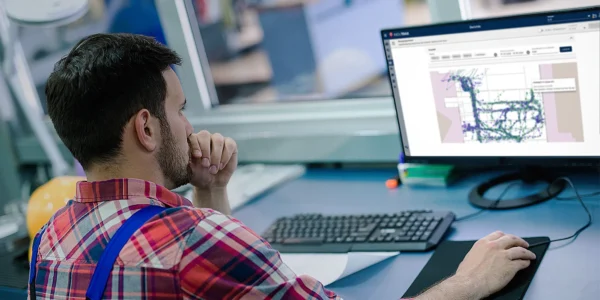
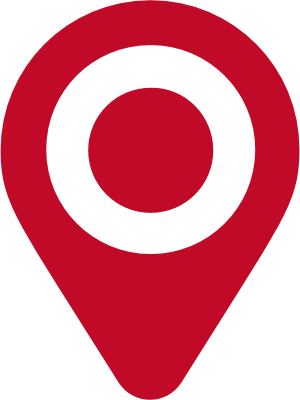
- Data-driven process histories for verifiable value stream analyses for concrete improvement measures
- Reliable movement histories of real events on the company premises
- Open storage for easy access with business analytics or process mining tools
- Various reports and key performance indicators (KPIs) with map-based visualizations
Would you like to experience our software live?
Tools and production aids: against shrinkage and disorder
Production resources are only useful where they are needed. Any effort to organize them first is a waste of time. Tools that are not returned to their storage location annoy employees and hold up processes. And tools that (with or without intent) take the wrong route off the company premises are missing in action and have to be written off. Targeted communication with employees is more efficient than warning signs - and in the event of an incident, finding is better than searching. This secures the stock.
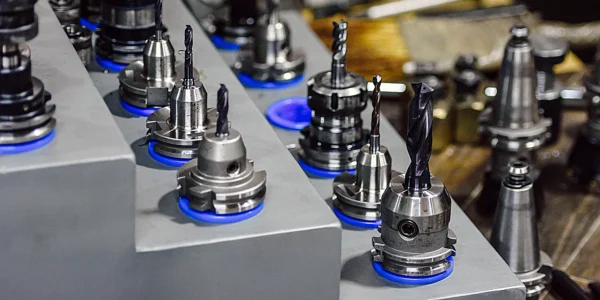
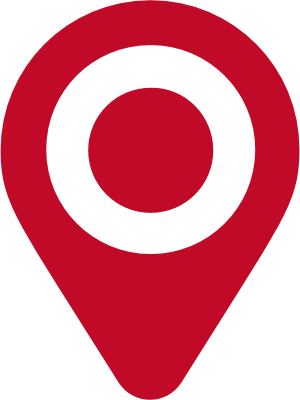
- Real-time visualization of object positions in maps for transparency about locations on the globe, on company premises and within halls
- Individually defined search criteria and display of results in list form (e.g. test equipment in rework with details of certification due)
- Early detection of bottlenecks or overcapacity of required resources
- Transparent tracking ofwhen, where and on which product a tool was used